Chapter 8
Aerospace Flights (1980-1986)
For NASA flight research, the 1980s opened with a significant administrative change —the Dryden Flight Research Center lost its independent status and became a directorate of Ames Reseach Center in 1981. This did not mean that NASA was downgrading flight research; on the contrary, several exotic programs emerged during the decade, and a variety of unusual aircraft continued to populate the skies above Edwards.
Given the cost of experimental flight aircraft and the evolution of increasingly sophisticated electronic and simulator systems, it was perhaps inevitable that NASA eventually turned to smaller, pilotless radio-controlled aircraft. In the 1980s, this idea was embodied in the HiMAT, a contraction of Highly Maneuverable Aircraft Technology. The HiMAT, powered by a General Electric J85 turbojet engine, had a length of 23 feet and a wing span of 16 feet.
The compact HiMAT was an evolutionary concept, originating during the M2 lifting body program of the 1960s. To test a variety of lifting body shapes in flight, an innovative NASA engineer at Edwards built a twin-engine radio-controlled model that carried the smaller test models high into the sky and made 120 test drops. Typical remotely piloted vehicles (or RPVs) used an autopilot system and had restricted maneuverability. The Edwards aircraft, on the other hand, was completely controlled from the ground, using instrument references. By the late 1960s, Edwards personnel were flying an actual lifting body test configuration,the Hyper III, in drop tests from a helicopter. Veteran fliers who flew the model by remote control found it a remarkable experience. “I have never come out of a simulator emotionally and physically tired as is often the case after a test flight in a research aircraft,” one pilot said. “I was emotionally and physically tired after a 3-minute flight of the Hyper III,” he admitted. Although remote flight research continued, demands of the YF-12 Blackbird program and other projects kept it at a low level. Still, significant progress occurred. The Edwards team took a Piper Twin Comanche fitted with an electronic fly-by-wire system, added a television system for a remote pilot, and turned it into a successful remotely piloted aircraft from takeoff to landing. Although a backup pilot flew in the cockpit, the remote operators practiced stalls, stall recoveries, and even made precise instrument landing approaches. In the early 1970s, these skills were translated into an applicable test program to investigate stall and spin phenomena after several fighter planes were lost in spinning accidents. NASA let contracts to McDonnell Douglas for three 3/8-scale models of the F-15. Each model cost $250,000; a full-sized plane cost $6.8 million. Piloted from the ground and released from a B-52 at high altitude, the model F-15 program yielded useful information for final revisions of the operational Air Force fighter. The remote pilots doing the flying found the spin tests quite challenging: the heart beats of pilots in normal, manned flights went from 70-80 per minute to 130-140 during the remotely piloted drop tests.
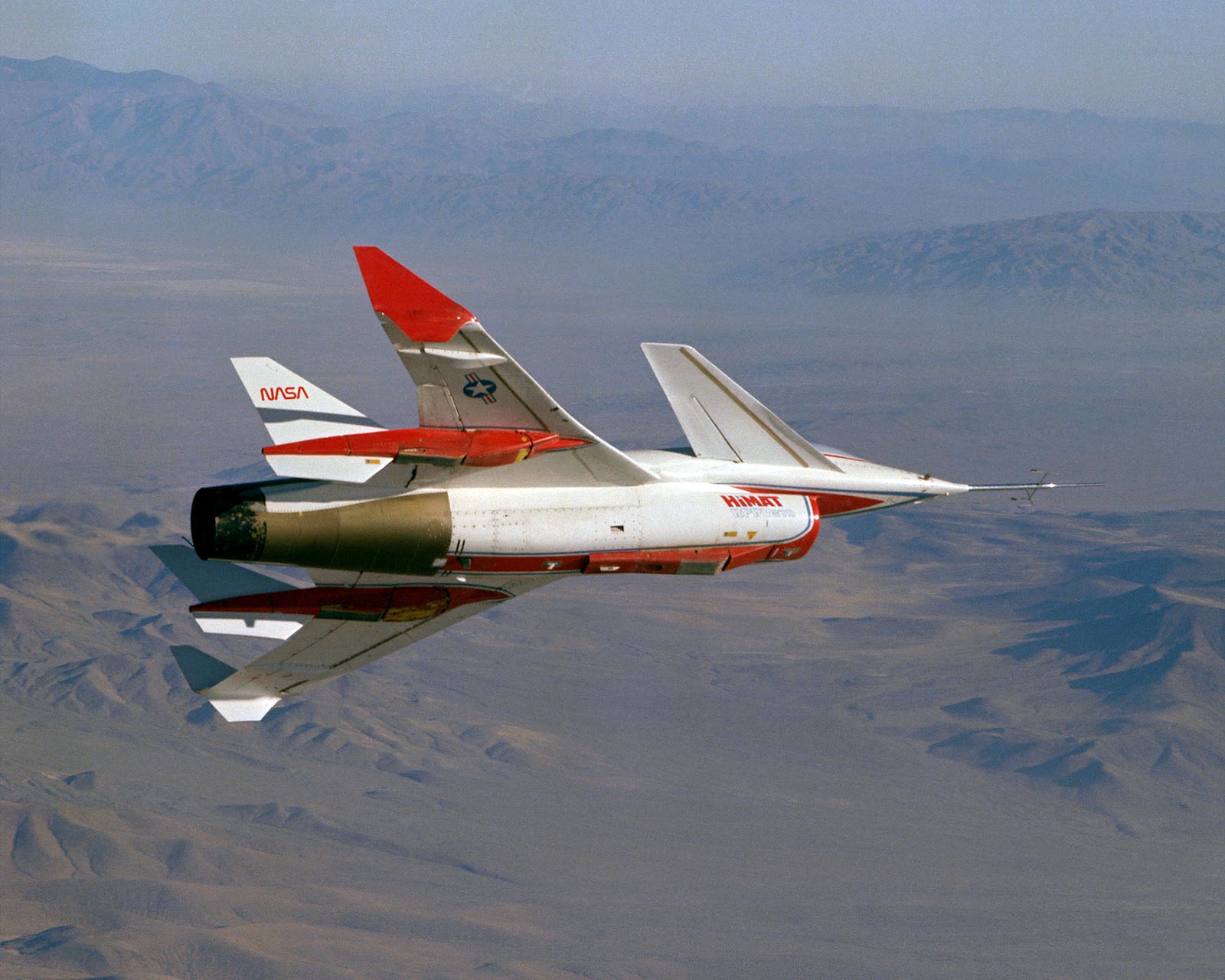
The remotely controlled flight tests were controversial. Extensive ground support systems were nearly as expensive for remote flight operations as they were for manned aircraft. Still, remotely controlled flights were useful; models offered a cost-effective method for testing esoteric designs; they were obviously advantageous in dangerous flight maneuvers. The positive factors were convincing as NASA and the military services pondered exotic configurations and materials of combat planes for the 1990s and beyond. The logic for a test vehicle like the HiMAT was unusually strong.
The HiMAT structure itself was composed of various metal alloys, graphite composites, and glass fibers. It had sharply swept wings, winglets, and canard surfaces —considered aeronautically avant garde when the first plane flew in 1978. Carried aloft by a B-52, the HiMAT was remotely —and safely— flown through a series of complex maneuvers at transonic speeds. The HiMAT was designed as a modular vehicle so that wings, control surfaces, and structural materials could be evaluated at a fraction of the cost of building a full-sized aircraft. The HiMAT’s changing configurations suggested the possible shapes of aircraft to come.
While the HiMAT continued to test alternative design ideas, flight test specialists nonetheless recognized the persistent value of full-sized manned aircraft. The result was the Grumman X-29, a plane whose dramatic configuration matched that of the HiMAT. The X-29 had a single, vertical tail fin and canard surfaces —not unique in the 1980s. What made the X-29 so fascinating was its sharply forward-swept wings.
The forward-swept wing had precursors in German designs of World War II. In 1944, Junkers put such an experimental jet into the air—the JU-287. The war ended before extensive flight tests could be carried out, but the JU-287 quickly revealed one of the major problems of any swept forward design: structural divergence. Lift forces on wings cause them to bend slightly upward. When the wings sweep forward, this force tends to twist the leading edge upward, increasing lift and the bending motion until the wing fails. One solution was to keep the wing absolutely rigid, but conventional metal construction made such wings so heavy they were impractical. Although swept forward wings occasionally appeared on various aircraft in the postwar era, construction and weight problems proved intractable. The solution appeared in the form of composites, affording wings of light weight but high strength.
Grumman had submitted an unsuccessful HiMAT design, which ran into severe wing-root drag problems. A forward-swept wing seemed to offer answers, and the company had quietly pursued the idea. NASA also became interested, and the DoD eventually agreed to support a radical new design. NASA became responsible for technical support and flight testing. In 1987, the plane was officially announced as the X-29, the first new ”X” aircraft developed by the United States in more than a decade. The fuselage took shape very quickly, since the forward section came from a Northrop F-5A. Landing gear came from the General Dynamics F-16A, and the engine was adapted from a General Electric power plant developed for the McDonnell Douglas F-18 Hornet. At first glance, the X-29 seemed a sorry aeronautical compromise, merely incorporating bits and pieces from other planes. But its wings and related design elements made it truly unique. Moreover, it was highly unstable.
When the X-29 made its first flight in 1984, the forward-swept wings and canard surfaces were its most distinguishing characteristics. In swept back wings, controllability became a problem as increasingly turbulent air flowed over the wing tips and tail surfaces. The X-29’s wing tips, however, were always moving in comparatively undisturbed air, enhancing controllability at high speeds, and the canard surfaces also operated in an air stream much less turbulent than that around the tail. The rigid wing of the X-29 owed much to composites and the way they were layered in relation to the angle of the wing and aerodynamic stresses, overcoming the tendency to structural divergence.
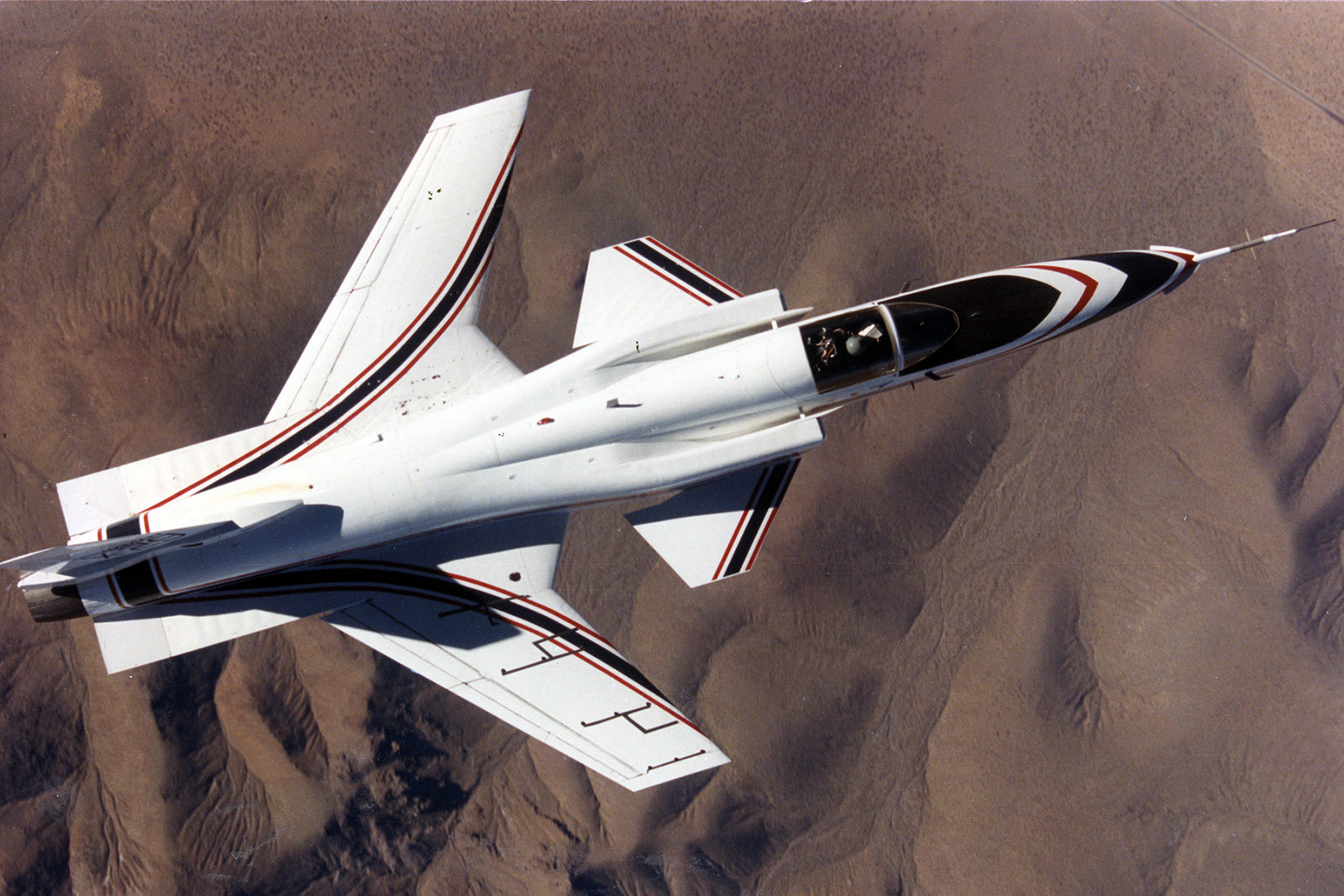
Among the electronic advances of the X-29, the most fascinating related to its inherent instability. Most planes were built to be stable in flight, returning to straight and level flight if diverted. In a dog fight, such placidity could be fatal. The F-16 jet fighter was built to be about 5 percent unstable, but the X-29 was built to be about 35 percent unstable. This extreme instability was more than any pilot could manage, so a trio of flight computers were developed to keep the plane under control while allowing the pilot a remarkable latitude in terms of maneuverability. At a rate of 40 times per second, the computers analyze the plane’s attitude and decide what is necessary to keep the plane under control while responding to the pilot’s inputs. This allows for some unusual flight maneuvers which could contribute to more agile combat planes in the future. For one thing, the X-29 could ”levitate” in flight —climbing while maintaining a straight and level attitude.
Exotic experimental military planes represented only one of several areas of NASA’s study. During the 1970s, the general aviation sector became increasingly robust. Most Americans knew little about this remarkably diverse segment of American aviation, which included all aircraft except those flown by commercial airlines and the armed services. There were about 2400 scheduled airliners in service during the 1970s and 4300 in the 1980s, while the general aviation fleet climbed from 150,000 to 220,000 aircraft, ranging from propeller-driven single engine planes to multimillion dollar executive jets. Sales of general aviation aircraft represented a significant contribution to America’s favorable balance of payments, since 90 percent of the world’s fleet of general aviation types originated in American factories. Given the scope of general aviation operations in the United States and the significance of American domination of the world market for this sector, NASA’s attention was probably overdue when the agency began comprehensive studies during the late 1970s. Results came very quickly as more than a dozen production and prototype designs incorporated features derived from relevant NASA studies.
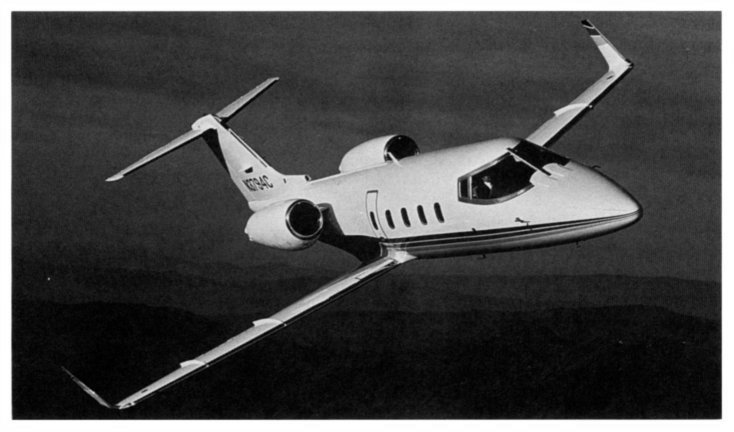
One distinctive hallmark of NASA’s general aviation investigations was the wingtip winglet, a device to smooth out distorted air flow, resulting in improved wing efficiency and enhanced fuel economy. During the 1980s, a number of high performance business jets, such as the Learjet, as well as late-model transports built by Boeing and McDonnell Douglas used this innovation. The agency also developed a new high performance airfoil for general aviation; the GAW-1. A separate research effort went into stall/spin problems, using radio-controlled scale models as well as several different full-sized operational aircraft. There were additional programs to probe exhaust and engine noise, engine efficiency, and the use of composites. A special investigation of crash survivability tested the airframes of planes as well as injuries to passengers, represented by carefully instrumented anthropomorphic dummies. A huge drop tower let the test planes plunge onto a typical runway; test results were useful to many aviation industry firms, including manufacturers of aircraft seats, seat belts, and body restraint systems.
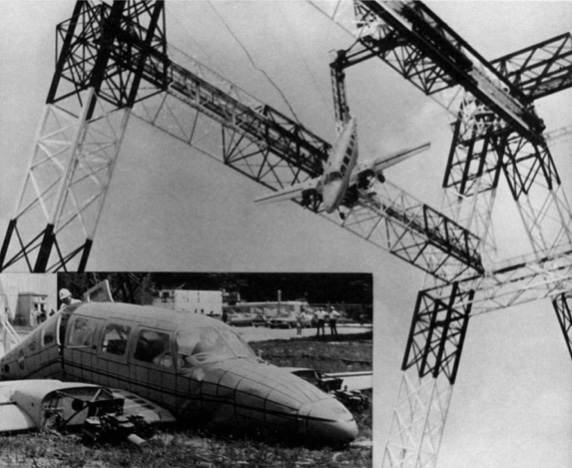