8. Airline to Space
The space transportation system is, broadly, the Shuttle Orbiter, fuel tank, and launch boosters plus everything that goes with it:
- Spacelab, in which scientists and technicians of many nations can conduct their own experiments beyond Earth’s gravity and atmosphere;
- Optional fight kits of special equipment and extra supplies, such as additional tanks of fuel for maneuvering, to enhance the Orbiter’s performance, and extend its stay in space;
- The payload manipulating arm described in Chapter 6;
- A modular spacecraft that can be outfitted with different sets of instruments for a variety of missions;
- Rockets to propel Shuttle payloads to higher orbits or on their way to other planets;
- A complex communications network;
- Launch sites and service facilities;
- Ingenious cargo handling equipment to speed ground operations;
- And the management structure to put them all together into a working system.
- Ground control centers;
The head of NASA’s Office of Space Transportation Systems, John F. Yardley, has compared the operation to running a scheduled airline with aspects of a chatter service.
Twenty to thirty percent of all Shuttle missions will carry some parts of Spacelab, a versatile orbiting laboratory for manned and automated research in the low-gravity, high-vacuum environment of space. In its laboratory module men and women working without space suits in a comfortable, Earth-like atmosphere will conduct scientific and technical experiments in close cooperation with colleagues on the ground. Its development is financed by ten European nations under the European Space Agency. Agreements with the United States provide that ESA design and build one Spacelab as well as its test and ground equipment. Others that may be ordered later will be paid for by the U.S. NASA is in charge of operations. The European countries involved are Austria, Belgium, Denmark, West Germany, France, Italy, the Netherlands, Spain, Switzerland, and the United Kingdom.
Like the Shuttle itself—but unlike Skylab-Spacelab is reusable, designed to be launched and returned with the Orbiter as many as fifty times over a life of ten years. It stays in the Orbiter throughout the flight, is exposed to space when the big cargo doors are open in orbit, and is removed on the ground for rearrangement of its elements and changes of instruments and equipment for different kinds of missions.
Spacelab’s main elements are the pressurized laboratory, which affords shirtsleeve working conditions, and an instru-ment-carrying platform called the pallet, a sort of open back porch, that exposes materials and equipment directly to space. Each of these is segmented for mission flexibility; either can be flown alone or in more than half a dozen different combinations with the other.
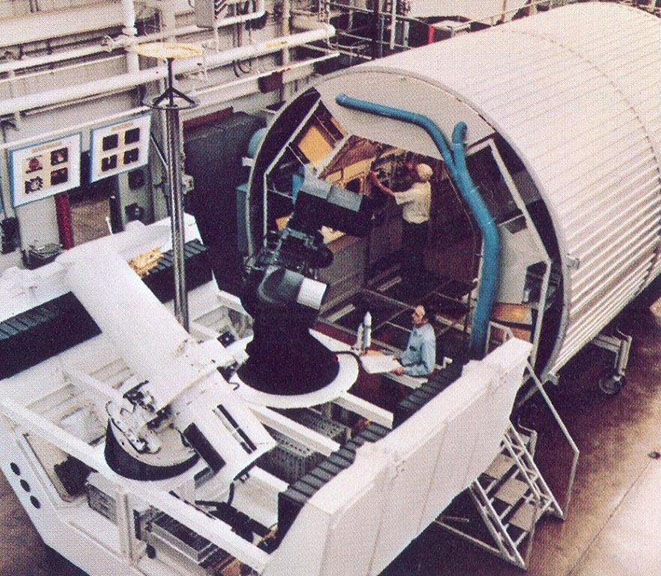
One segment of the laboratory module, called the core segment, houses data processing equipment and utilities for both the pressurized modules and the pallets when flown together. It also has usual laboratory fixtures-air-conditioned experiment racks, work benches, and so forth. The second, called the experiment segment, provides more pressurized working space, racks, and benches. Each pressurized segment is a cyclin-der 4.1 meters in diameter and 2.7 meters long (13 ft by 9 ft). When the two are assembled, with their cone-shaped end sections, the maximum outside length is 7 meters (23 ft).
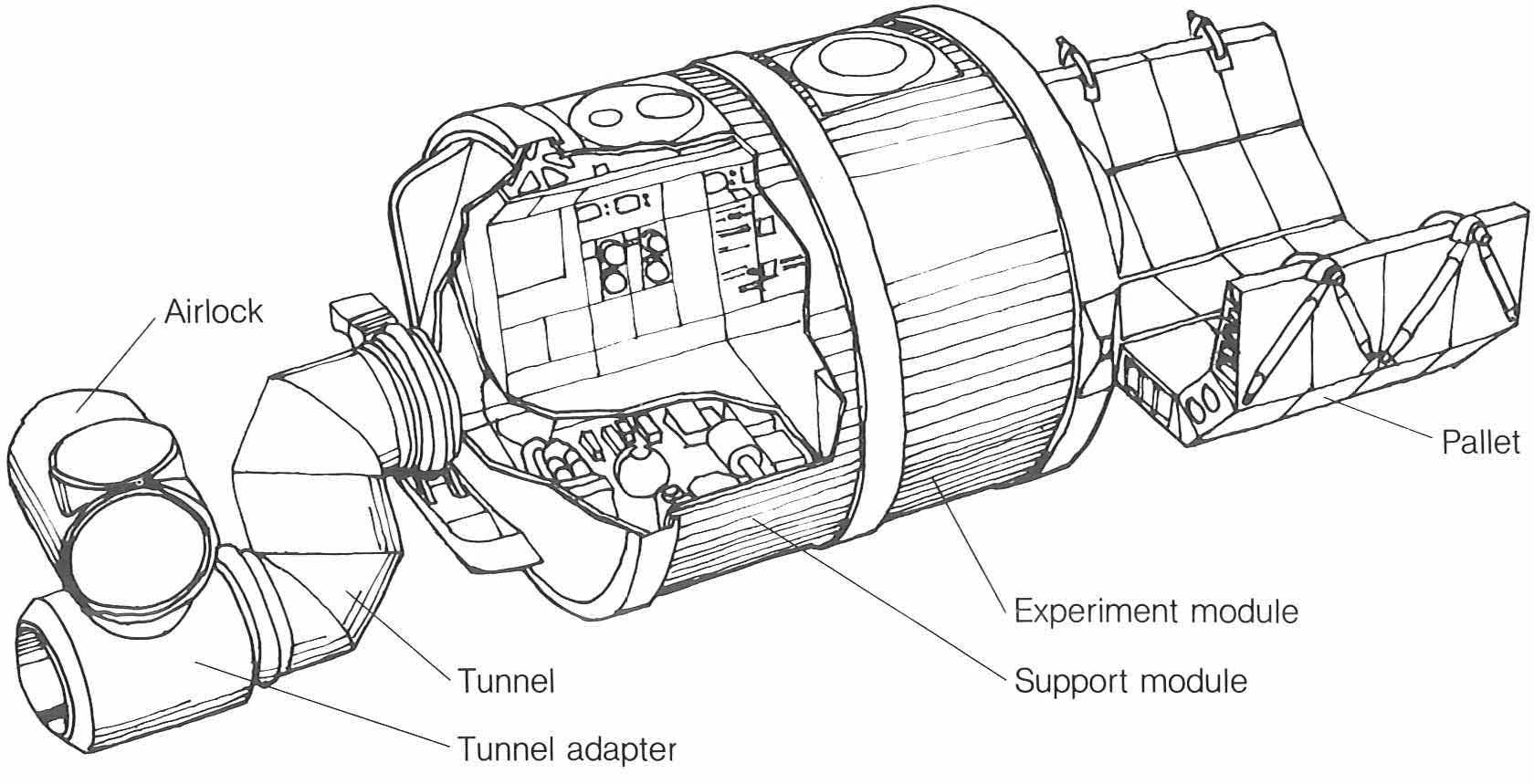
As many as five pallet segments can be flown at one time, each three meters (10 ft) long. They serve not only as platforms for mounting instruments but also can cool equipment, provide electrical power (generated by one of the Orbiter’s three fuel cells), and furnish connections for commanding experiments and acquiring data from them. When pallets alone are used, equipment for essential services for the experiments, such as a power distribution box and computers, are protected in a small pressurized, temperature-controlled housing called the igloo. Equipment and experiments can be serviced, if necessary, by astronauts in space suits. The pallets are used for large instruments telescopes, antennas and experiments that require direct exposure to space or need unobstructed or broad fields of view. An instrument-pointing system provides attitude control and stabilization for experiments that require more precise pointing than is possible with the Orbiter controls. Pallet experiments can be controlled from the laboratory module or the Orbiter flight deck or from the ground through the Orbiter’s communications links.
The laboratory module can accommodate three people regularly and a fourth for brief periods, such as a change of shifts. Handholds, handrails, and foot restraints help them work in the most convenient body position and move about safely. The overhead structure contains lights and air ducts. The air is at sea-level pressure, as in the Orbiter, and is kept at 18 to 27° C. At the work benches are electrical outlets, laboratory-wipe dispensers, writing instruments, paper, and storage compartments for equipment like microscopes, centrifuges, incubators, materials-processing furnaces, and photographic apparatus. There are view ports and, in the top, an optical window and an airlock, a meter in diameter, for extending materials and sensors into space and retracting them.
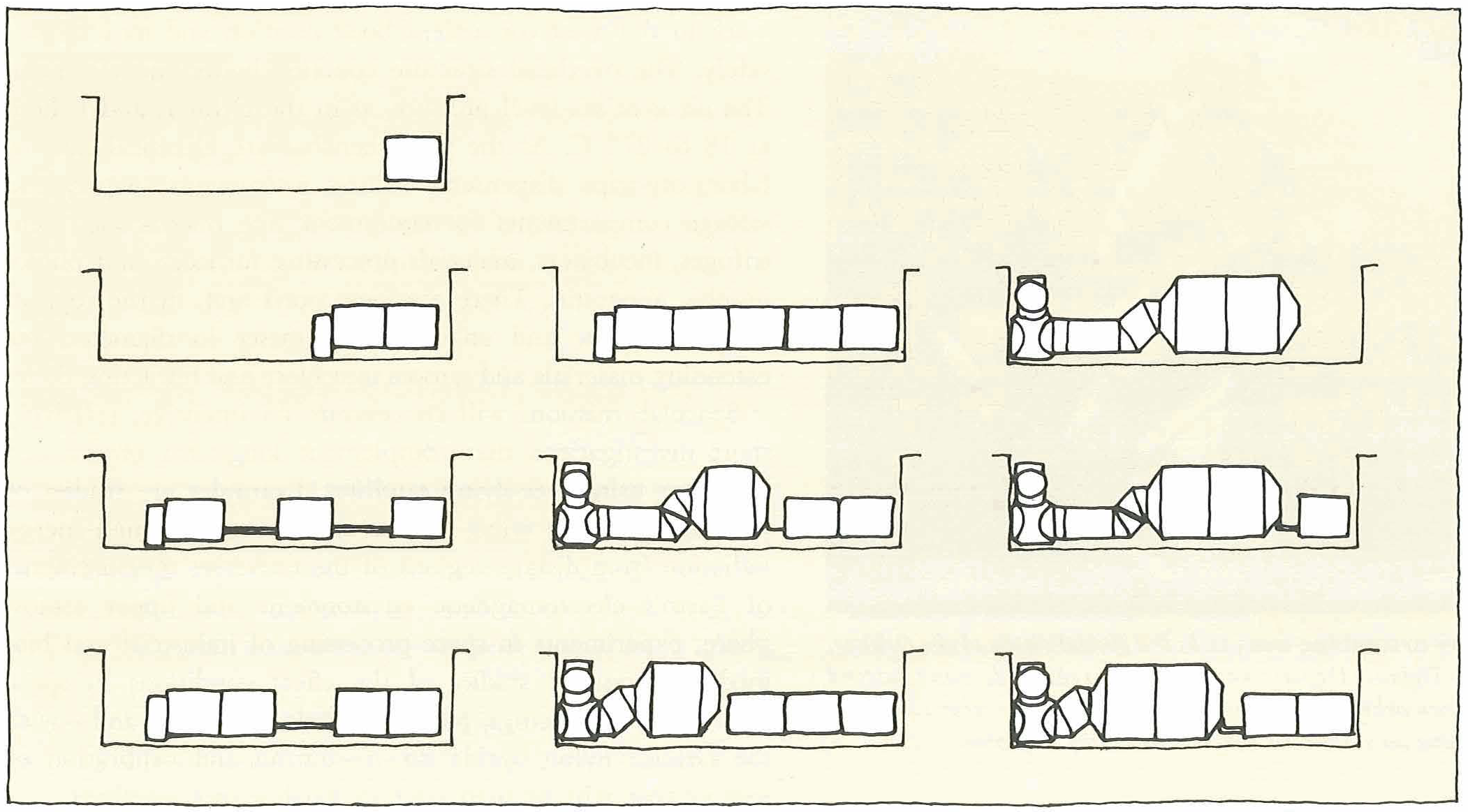
Spacelab missions will concentrate on intensive, relatively short investigations that complement long-term observation programs using free-flying satellites. Examples are studies of the Sun and solar wind, comets and novas, and high-energy radiation from distant regions of the universe; measurements of Earth’s electromagnetic environment and upper atmosphere; experiments in space processing of industrial and biomedical products; studies of the effect conditions in space have on human beings, plants, animals, and cells; and with the Orbiter flying upside down-testing and calibration of sensors that will be used later in Earth-survey satellites.
A pressurized tunnel leads from the laboratory module to the Orbiter cabin, where the experimenters, called payload specialists, will live when off duty. Unlike the basic Shuttle flight crew commander, pilot, and mission specialist—payload specialists need not be career NASA astronauts. They are scientists or technicians in reasonably good health chosen, with NASA approval, by the designers and sponsors of the instruments and experiments to be flown. NASA gives them several weeks of classroom instruction and training in fight simulators to acquaint them with the Shuttle and its equipment, living and working conditions in space, safety and medical procedures, and their roles in cooperation with other members of the crew in carrying out the planned mission. The first five selected for training were two Americans and three Europeans: German, Swiss, and Dutch.
The Multimission Modular Spacecraft, although not classified by NASA as part of the Space Transportation System, is a versatile new unmanned workhorse to be carried into space in the cargo bay of the Shuttle. Designed to take advantage of the Shuttle’s unique capabilities, it will carry its own propulsion, stabilization, and guidance equipment. It can rendezvous with the Shuttle for servicing in orbit or for return to Earth for overhaul. Fitted with interchangeable instrumentation, the MMS can take on a variety of missions oriented toward Earth, the Sun, or stars. A considerable proportion of all automated satellite programs of the 1980s may use it.
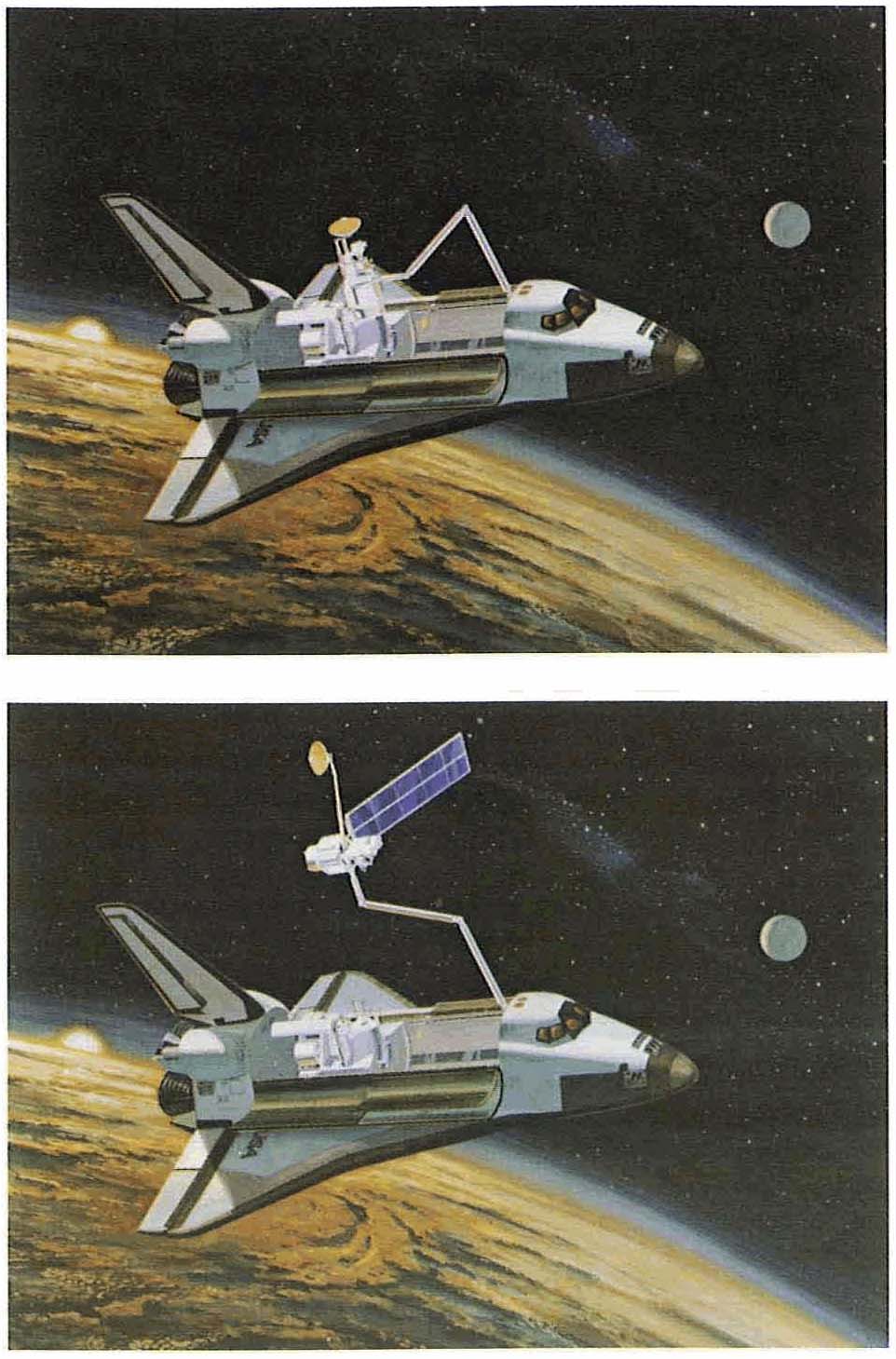
The spacecraft is a load-carrying structure with modules attached for power, communications and data handling, and attitude control. Propulsion motors for changing orbits, solar power arrays, and various kinds of antennas can be added. It is deployed from the Orbiter and recaptured for servicing or return by the mechanical cargo-handling arm. For servicing and updating in orbit, instruments can be removed and stowed and replacements inserted by mechanisms controlled from the Orbiter flight deck.
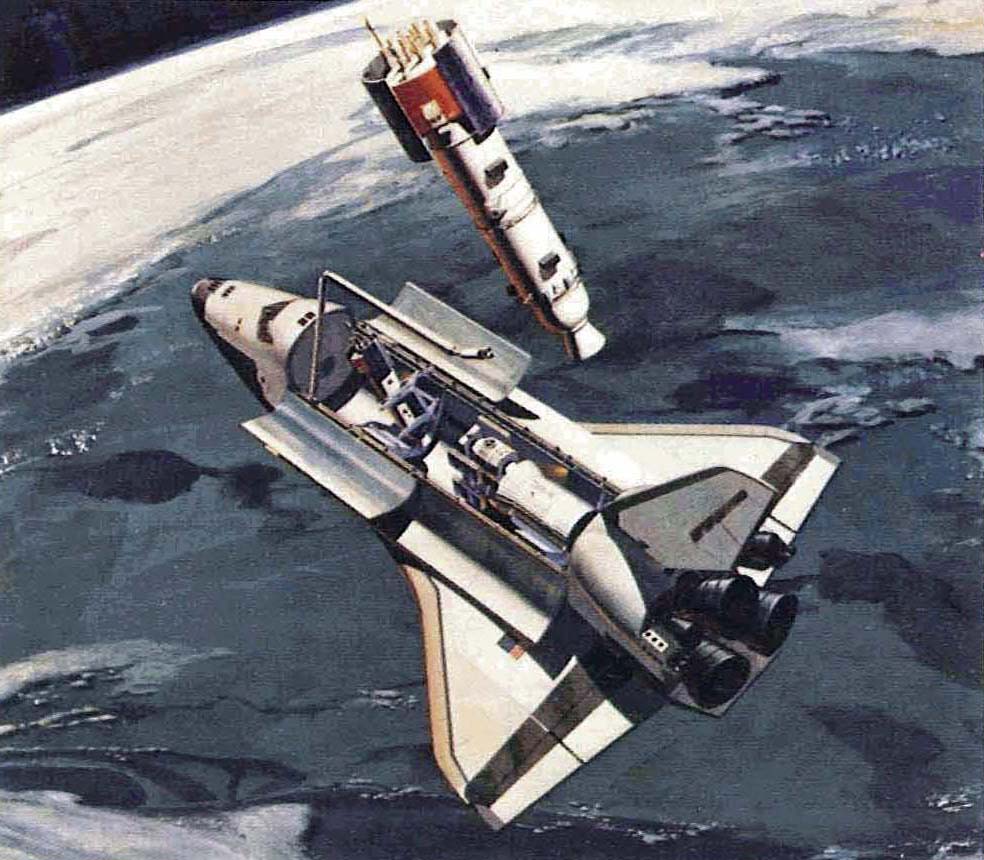
Two low-cost, expendable boosters are being produced to propel spacecraft deployed from the Orbiter to altitudes beyond its reach. They’re called upper stages, since they do the work performed by the final, top stages of earlier launch vehicles. Both are solid-propellant rockets that come in different sizes and combinations for small to large payloads destined for missions near and far.
For a launch from the Shuttle, the upper stage and attached spacecraft are pointed in the right direction by the Orbiter’s attitude-control thrusters, and are then gently ejected by springs. At the proper place in the circular orbit to achieve the desired destination (over the Equator, for example, to reach geosynchronous orbit), with the Orbiter maneuvered to a safe distance, the upper stage is ignited by radio command or a timer to increase velocity and raise the trajectory.
The simpler of these boosters, developed by industry as a commercial venture for sale to NASA and other users, is the Spinning Solid Upper Stage, so named because its stability and direction in flight are maintained simply by spinning, like a gyroscope. ’The rocket and spacecraft together are spun up mechanically as high as 100 revolutions per minute, depending on size, before being released from the Orbiter. Two sizes are designed to lift payloads of about 1100 kilograms or about 2000 kilograms (2400 lb or 4400 lb) to high transfer orbits, with the spacecraft then providing propulsion for final injection into geosynchronous orbit. Final weights on station will be about 550 and 1000 kilograms (1200 and 2200 b) respectively. Four of the smaller spinning solid upper stage or two of the larger model, with their spacecraft, can be carried on a single Shuttle flight. One or two may also share a flight with other payloads.
A huskier booster, the Inertial Upper Stage, is being developed by the U.S. Air Force for use with both military and civilian spacecraft. As the name implies, it has a built-in guidance and propulsion system for stability and flight control. Using two or three solid rocket motors, it can place heavy loads-2270 kilograms (5000 lb) or more-in geosynchronous or other high-altitude orbits. It can also inject spacecraft into trajectories for the Moon or planets.
One of the first assignments for the Inertial Upper Stage will be to place in geosynchronous orbit Tracking and Data Relay Satellites to handle communications among all elements of the Space Transportation System. Space operations in the past have depended mainly on ground stations and tracking ships for communications, and there were large blind spots in their coverage. Crews of manned spacecraft were out of touch with Mission Control for part of every orbit, and satellites frequently had to record data on board and transmit them to Earth later when within range of a receiving station.
Two Tracking and Data Relay Satellites, one on the Equator off Brazil and one over the Pacific Ocean, and a single ground station at White Sands, New Mexico, make it possible to track and communicate with the Orbiter and most orbiting spacecraft for 85 to 98 percent of the time. Several tracking stations and tracking ships can be eliminated, and there will be less need for on-board tape recorders—often a trouble-prone part of a satellite.
The Tracking and Data Relay Satellites will be supplemented by the remaining stations of the older global space tracking and data network, and the NASA ground communications network, perhaps augmented by domestic communications satellites, will continue to link the tracking stations and control centers.
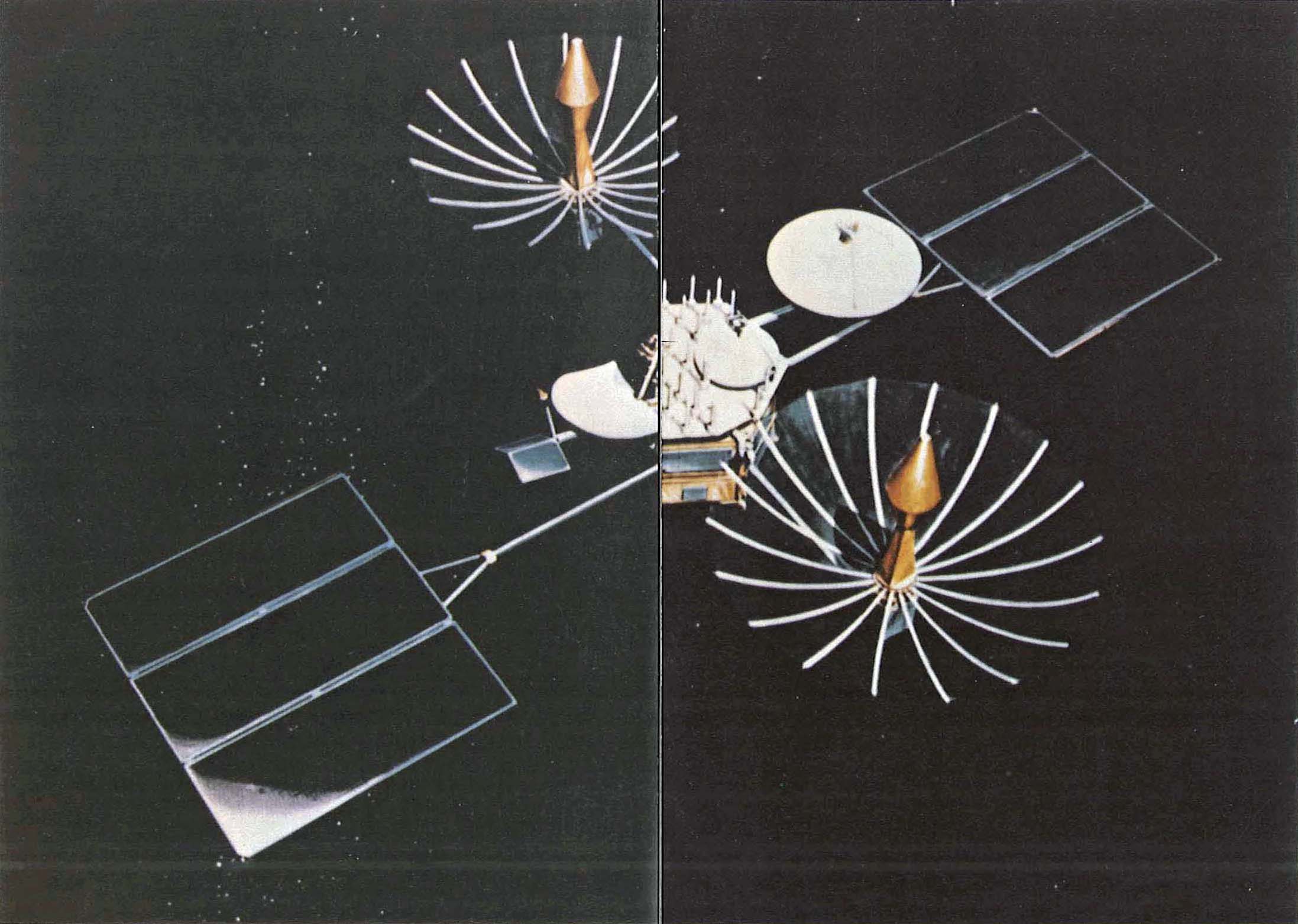
During operations in orbit, communications with the Orbiter are maintained, as in previous manned flights, by the Mission Control Center at the Johnson Space Center near Houston, Texas. Experiment ground controllers will communicate with payloads through the Orbiter as long as these are attached to it. After separation, communications with free-flying satellites in Earth orbit will go to and from a Payload Operations Control Center at the Goddard Space Flight Center, in Maryland, near Washington, D.C. One at the Jet Propulsion Laboratory in California, near Los Angeles, controls spacecraft headed for the Moon or planets through NASA’s Deep Space Network. Payloads that remain attached to the Orbiter, including Spacelab, are monitored from a Payload Operations Control Center in the same building with Mission Control, which provides separate voice channels for science and Orbiter operations and television channels shared by the flight crew and payload specialists.
Launches of early Shuttle missions, both civilian and military, are from the Kennedy Space Center, Florida, out over the Atlantic Ocean to avoid flying over populated areas in the critical first minutes. This direction also gives space-bound vehicles an extra velocity assist from Earth’s eastward rotation. The payloads from here include all communications satellites and others for geosynchronous orbit. Missions requiring north-south (polar) orbits, including many weather and Earth-survey satellites, are launched southward over the open Pacific from Vandenberg Air Force Base, on a point of the California coast.
Ground operations at the two bases are similar. Using procedures like those of commercial airlines, such as servicing the engines without removing them, ground crews working two shifts are expected to have an Orbiter ready for relaunch in as short a time as two weeks after return to Earth. The planned goal, when the Space Transportation System is fully operational and running smoothly, is 160 working hours: an hour at the landing runway for the crew to debark, for a quick safety inspection, and hooking up air-conditioning equipment and a tow tractor; 90 hours in the Orbiter Processing Facility for post-landing safety procedures, removing any returned payloads, inspecting and servicing of the spacecraft, and installing the new payload; 45 hours in the Vehicle Assembly Building for hoisting the Orbiter to a vertical position and mating it with a new External Tank and refurbished Solid Rocket Boosters; and 24 hours for moving the assembled space vehicle on the mobile launching platform to the launch pad, installing any hazardous or extra-sensitive payloads here rather than earlier, loading propellants, getting the new crew on board, and final checks during a two-hour countdown to liftoff.