Apollo 4: The Trial Run
The Significance of AS-501
The problems of the spacecraft threatened, but did not extinguish, the hopes of reaching the moon within the decade. Much depended on the outcome of the first Saturn V mission. If the largest launch vehicle and launch complex yet built both performed satisfactorily, the Apollo program could still meet its schedule.
A successful mission would achieve several significant goals. It would mark: the first launch from launch complex 39, the first flight of the integrated Apollo-Saturn V space vehicle, the initial trials of the first (S- IC) and second (S-II) stages of the Saturn V launch vehicle, the first shutdown and restart in space of the third stage (S-IVB) engine, and the first demonstration of the Apollo spacecraft’s ability to reenter the earth’s atmosphere at the speeds and temperatures it would reach on return from a mission to the moon. Many other benefits would accrue if the unmanned earth-orbital mission succeeded. The adequacy of ground tracking, telemetry, and communications operations at stations around the world could be evaluated. The launch vehicle stages and spacecraft modules would carry additional research and development instrumentation to measure the performance of their internal components. A total of 4,098 in-flight measurements - about 2/3 of them for the launch vehicle, 1/3 for the spacecraft - were scheduled.1
The results of this mission would confirm or deny the validity of a major management decision made in the fall of 1963-the use of all-up flight testing. Designed to result in an overall time saving, all-up testing meant that all launch vehicle stages and spacecraft modules (essentially in their final configuration) would be tested together on each flight. Previous practice had favored a gradual buildup of subsystems, systems, stages, and modules in successive flight tests.2 Based in part on the unqualified successes of the first four Saturn I missions, but made before any Apollo spacecraft had flown, the eggs-in- one-basket decision involved a calculated risk. Success in all-up testing was the quickest way to accomplish a manned lunar landing. On the other hand, failure of the first Saturn V mission would be a major catastrophe.
For KSC the first flight of the Apollo-Saturn V had a narrower, but more important, objective than that of the total mission. For the first time the facilities, equipment, procedures, and checkout crews would be put to the test. The 500-F facility checkout tests had instilled a certain degree of confidence (while revealing much that remained to be done), but this would be “the real thing.” This time, every action would lead toward those moments when the first-stage engines would ignite, the hold-down arms on the launcher platform would retract, and the Apollo-Saturn V vehicle would be committed to flight. In the process of receiving, assembling, testing, and launching this first Apollo-Saturn V, KSC civil service managers and the launch vehicle, spacecraft, and launch support contractor crews would be learning to work together as a unit. It would prove a difficult task for all concerned - and not without its rough moments - but, in the end, a well-functioning launch team would be the reward.
The Parts of AS-501
The first of the Apollo-Saturn V space vehicles had received its official designation in April 1965 when Maj. Gen. Samuel C. Phillips, Apollo Program Director, announced: “Apollo flight missions to be flown on Saturn IB and Saturn V will be designated as Apollo/Saturn followed by the number of the launch vehicle assigned to the flight mission (i.e., Apollo/Saturn 201, Apollo/Saturn 202, etc., and Apollo/Saturn 501, Apollo/Saturn 502, etc.).”3 The AS-501 space vehicle consisted of Saturn V launch vehicle number 501 and Apollo spacecraft number 017. The launch vehicle had three stages and an instrument unit. The spacecraft included a spacecraft lunar module adapter, a lunar module, a service module, a command module, and a launch escape system.
Components of the AS-501’s first stage (S-IC) were constructed by the Boeing Company at Michoud, Louisiana, and assembled at the Marshall Space Flight Center in Huntsville, Alabama. The S-IC stage consisted of a structural framework to which the engines were attached, an RP-1 (kerosene) fuel tank, a LOX (liquid oxygen) tank, an intertank structure separating the fuel and LOX tanks, and a forward skirt that connected to the second stage. The five Rocketdyne F-1 engines would develop a total of 33.4 million newtons (7,500,000 pounds of thrust) at liftoff. The center engine was fixed in position, but the others were mounted on gimbals to provide attitude control and steering for the vehicle. Two hydraulic actuators swiveled each engine in response to signals from the flight control computer located in the instrument unit. In less than 3 minutes of powered flight, the first stage engines would consume almost 2,000 metric tons of propellants. Eight small solid-propellant retrorockets were attached to the framework to slow the first stage after engine shutdown, guaranteeing separation of the first and second stages.
The second stage (S-II), built by North American Aviation, Inc., Canoga Park, California, consisted of an aft interstage, an aft skirt and framework to which the engines were attached, integral LOX and liquid hydrogen (LH2) tanks with a single common bulkhead, and a forward skirt. The five Rocketdyne J-2 engines were arranged similarly to those of the first stages, with the center engine fixed and the four outer engines gimbaled by hydraulic actuators in response to signals from the instrument unit. The aft interstage, which surrounded the rocket engines, was the means of attaching the second stage to the first stage; it also supported the weight of the second and third stages and the spacecraft. In flight when the first and second stages separated and the second stage engines ignited, the aft interstage was jettisoned. During the second stage’s 6 minutes of powered flight, the five J-2 engines would consume about 425 metric tons of propellants while developing nearly 4.5 million newtons (one million pounds of thrust).
The third stage (S-IVB) of the launch vehicle was built by Douglas Aircraft Company. It consisted of the aft interstage, an aft skirt, a thrust structure to which the single J-2 engine was attached, a LOX tank and an LH2 tank, and a forward skirt. Because the third stage was smaller in diameter than the first and second stages, the aft interstage tapered from a diameter of 10 meters at its base to 6.6 meters where it joined the aft skirt. The single Rocketdyne J-2 engine would develop 889,600 newtons (200,000 pounds of thrust) and was capable of being shut down in space, and then reignited. Hydraulic actuators gimbaled the engine, in response to signals from the instrument unit, to provide pitch and yaw control during powered flight. Two self-contained auxiliary propulsion system modules, mounted 180 degrees apart on the aft skirt, would provide roll control during powered flight, and pitch, yaw, and roll control while the J-2 engine was shut down. During the approximately 7 1/2 minutes of third-stage powered flight (including first and second burns), about 105 metric tons of propellants would be consumed.
IBM’s instrument unit (S-IU), atop the third stage, was 6.6 meters in diameter, slightly less than one meter in height, and weighed about 10 metric tons. The unit consisted of segments of honeycomb material sandwiched between inner and outer skins and looked like a narrow collar or ring that had been slipped part way down the vehicle. Mounted on the inner skin were 16 cold plates, each 76 centimeters square. Coolant fluid circulated through these plates to dissipate heat generated by the operation of the guidance and control, instrumentation, and electrical power and distribution equipment installed on them. By attaching the equipment to the skin, space was left in the center for the domed bulkhead of the third-stage liquid-hydrogen tank, which extended into the instrument unit, and for the landing gear of the lunar module to be included on later missions.4
The flight plan called for the Saturn V to place the spacecraft and third stage into a circular orbit. After completing two orbits, the third stage would ignite a second time. Separating from the third stage, the spacecraft would rise to an apogee of approximately 18,500 kilometers by firing its service propulsion system engine. A second firing during descent from apogee would boost the command module’s reentry velocity to 11,075 meters per second or 40,234 kilometers per hour. Protected by its heat shield, the command module would reenter the atmosphere and return to earth northwest of Hawaii.
Delay after Delay after Delay
Apollo 4 was not ill-starred. In fact, it eventually went into space trailing a sizable cloud of glory. But no mission was so plagued by vexatious delay, due in part to the teething troubles of a new rocket and new stages, especially the S-II; in part, to the aftermath of the fire; and in part, to the all-up procedure which put a premium on prelaunch preparations. The delays were not unproductive. Many involved the learning of lessons that, once mastered, were needed in succeeding Saturn V launches. Some serious problems did not delay the launch. For example, early in the checkout LC-39’s LOX line ruptured, threatening to hold up operations for several weeks [see chapter 15-9]. The line was repaired, and could have been repaired two or three times over, while other and more serious problems were being solved.
In mid-1966 General Phillips hoped to launch the first Saturn V early the following year. Few Apollo officials were very confident about the target date. The S-II second stage had become the pacing item in the program. Development problems had already delayed its delivery at KSC from July to October 1966. On 13 August the S-II reached the Mississippi Test Facility, only to be held up again when technicians found cracks. The discovery delayed the acceptance firings and forced Phillips to reschedule the arrival of the S-II stage at KSC for mid-November. That month the Apollo Program Office issued a revised schedule calling for delivery of the S-II stage at KSC on 9 January, with launch three months later. Meantime, checkout of the 501 vehicle proceeded without S-II. In its place the launch team employed a spacer, referred to as the “spool” because of its shape - a cylinder that flared out at both ends. With the spacer the launch team could stack the stages and begin checkout in the assembly building. The spool also gave KSC the opportunity to test handling equipment for the second stage.5
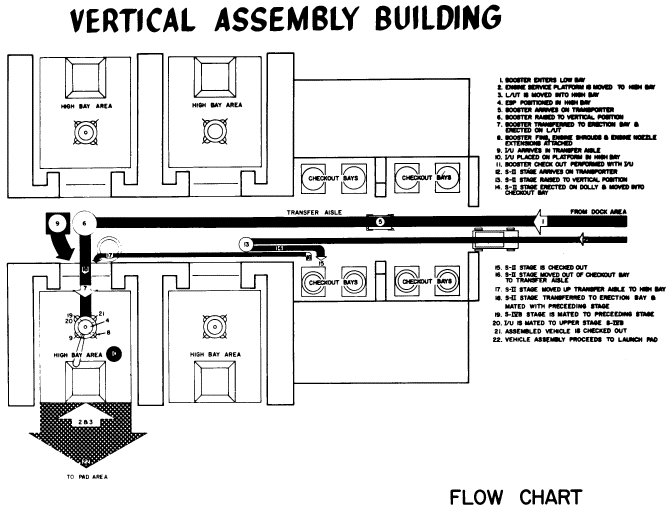
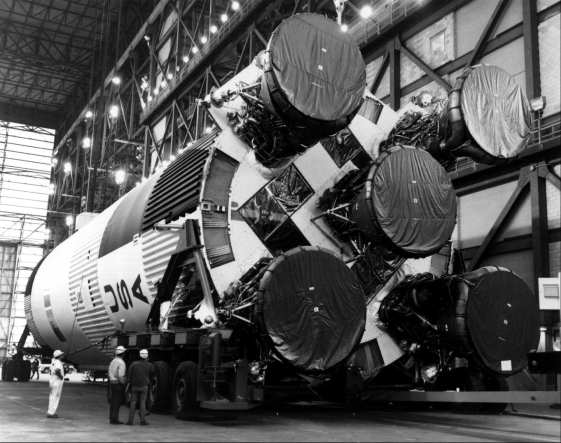
The third stage (S-IVB) was the first major component of Apollo 4 to be delivered at KSC. It arrived from Sacramento aboard the Guppy aircraft on 14 August 1966 and went immediately into a low bay of the assembly building for inspection and checkout. The following week the spacer and instrument unit arrived. On 12 September, as Peter Conrad and Richard Gordon prepared to blast off in Gemini 11, the barge Poseidon sailed into the Banana River with the first stage. Boeing gave it a lengthy checkout in the transfer aisle of the high bay before erecting the booster on 27 October. During the following week, technicians stacked the remaining launch vehicle stages, using the spool for the absent S-II. There were a few problems - the checkout of the swing arms took an extra two days and a cooling unit for the instrument unit sprang a leak - but the launch team, still counting on the mid-November delivery date for the S-II, hoped to roll the complete vehicle out to pad A by 13 January 1967.6
By late November the Apollo Program Office had moved the S-II’s arrival back to January, and the launch back to April. Since spacecraft 017 would not arrive for another three weeks, KSC erected the facilities verification model of Apollo on 28 November. This allowed North American to check out some of its spacecraft support equipment. The first week in December the memory core in a digital events evaluator failed after intermittent troubles; cracked solder joints were blamed. A hurried repair put the computer back on line.7
The command-service module arrived at KSC on Christmas Eve and was mated to the launch vehicle on 12 January 1967. That tardy prima donna, the S-II stage, finally appeared on 21 January. Tank inspection, insulation, and engine work were in progress by the 23rd. Test crews found damaged connectors on three recirculation pumps and set about investigating the extent of the rework that would be necessary. While inspecting the liquid hydrogen tank on the second stage, the North American team found 22 cracked gussets. These triangular metal braces, used to support the horizontal ribs of the stage framework, had to be replaced. Plans to move the second stage into a low bay checkout cell on the 29th were temporarily set aside because of a late shipment of the aft interstage (the cylindrical aluminum structure that formed the structural interface between the first and second stages). The interstage arrived on 31 January, and by the end of the next day the stage was in a low bay cell with work platforms around it.8
Despite the delay with the S-II stage, KSC officials expected to meet the new launch date in May. The fire on 27 January placed all schedules in question. Although Apollo 4 was an unmanned mission, NASA officials wanted to give command-module 017 a close examination. On 14 February, a week before the S-II could be inserted into a fully assembled vehicle, the spacecraft was removed from the stack and taken to the operations and checkout building. When inspection disclosed a number of wiring errors, KSC’s Operations Office cancelled the restacking of the spacecraft. By 1 March electrical engineers had discovered so many wiring discrepancies that the test team stopped their repair work, pending a thorough investigation of all spacecraft wiring. Within two weeks the North American and NASA quality control teams recorded 1,407 discrepancies. While North American repaired about half of these on the spot, modifications, repair work, and validations continued into June. During the break technicians performed pressure tests on service module systems at pad 16. It would be mid-June, with the wiring modifications for the command module finally completed, before North American could remate the spacecraft and take it back to the assembly building.9
As the extent of the wiring problems was not immediately recognized, the launch vehicle team forged ahead to recoup the time lost on the S-II stage. In mid-February Boeing’s airframe handling and ordnance group removed the instrument unit and spacer from the 501 stack and on the 23rd erected the S-II. The operation involved incredibly close tolerances. To qualify crane handlers, Stanley Smith, Bendix senior engineer of the crane and hoist group, stated, “We give them a technical examination and then check their reflexes and response to commands in training sessions.” During a mating, an operator and an electrician boarded the crane and another man helped guide movements from the floor by communicating with the operator via a walkie-talkie. Smith set a high goal for his team: “We strive to train our men to the point where they could conceivably lower the crane hook on top of an egg without breaking the shell.”10
After a stage was properly aligned on the Saturn stack, a crew of one engineer, two quality control inspectors, one chief mechanic, and eight assistants took eight hours to complete the mating. Three 30-centimeter pins on the second stage fitted into brackets located 120 degrees apart on the periphery of the first stage. Then the mechanics inserted 216 one-centimeter, high-strength fasteners into matching holes around the perimeter where the two stages joined. The team torqued the fasteners in a staggered sequence to secure the bolts evenly and ensure a uniform distribution of stress. The mating of the second and third stages was conducted in much the same manner.11 The 501 was now set up except for the missing CSM.
The lengthy delays with the flight hardware aided the Site Activation Board in its efforts to get LC-39 ready for its first launch. The board’s first flow [see chapter 15] included firing room 1, mobile launcher 1, high bay 1, and the other facilities required for the support of Apollo 4 - 1,280 activities altogether. During the first quarter of 1967, PERT charts showed less than 1% of these activities behind schedule. The decision in mid-April to modify the LOX system on launcher 1 and pad A put five weeks of negative slack into the site activation schedule. The modifications were made necessary by excessive pressure in the LOX system. KSC engineers added an automatic bleed system, relief valve supports, and a block valve that prevented purging through the drain line. As continued vehicle problems further delayed the rollout, the five weeks of negative slack disappeared.12
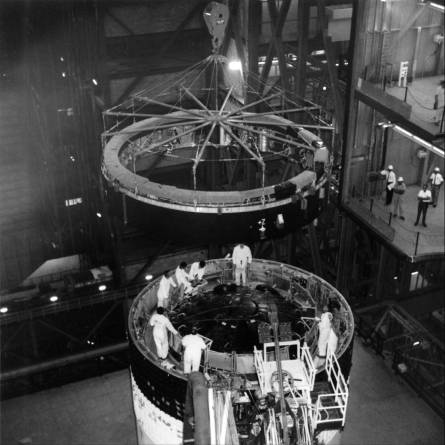
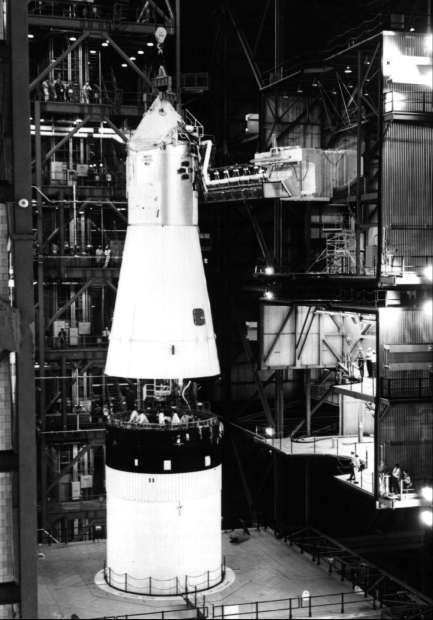
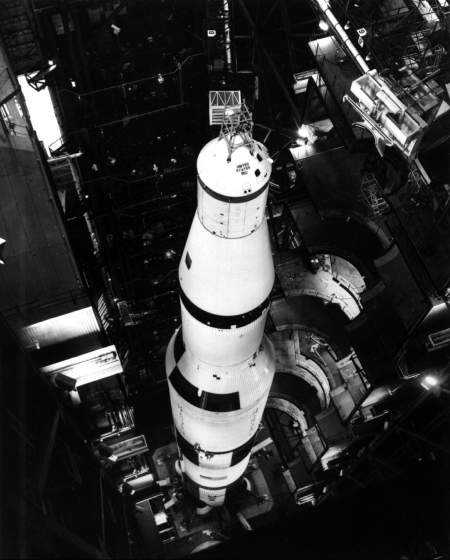
On 24 May the S-II stage was in trouble again. NASA announced it would be dismantled for inspection, consequent on the discovery of hairline cracks in the propellant tank weld seams on another S-II at the factory in California. The additional checks were not expected to delay the flight of 501 “more than a week or so.” By mid-June the inspection, which included extensive x-ray and dye penetrant tests, was completed and the stage returned to the stack. On 20 June, the command-service module was mechanically mated to the Saturn V, and 501 was - at last - a fully assembled space vehicle. A revised schedule on 21 July set rollout for mid-August. On 26 August 1967, the big rocket emerged from the high bay slightly more than a year after its first components had arrived at KSC, and a good six months after its originally scheduled launch date. It had been a year of delay and frustration, and the end was not yet.13
The Tests
While KSC officials were fighting the seemingly endless delays with the S-II stage and command module wiring, the launch team was putting Apollo 4 through the tests that would verify its flight readiness. The 456 tests in the Apollo 4 catalog fell into nine categories: electrical networks (90); measuring, fire detection, etc. (49); telemetry (27); RF and tracking (21); gyroscopes, navigation, control, and ground operations computers (86); mechanical and propulsion (146); combined systems (9); launch support equipment (13); and space vehicle (15).14
Saturn V tests, like those of the Saturn I and IB, progressed from component and subsystems tests, through systems, to combined systems or integrated tests. Hans Gruene’s launch vehicle operations team began by checking out the various pieces of support equipment in the low and high bays. The “ESE qualification test, low bay” was a typical procedure. As the initial KSC checkout of the low bay’s electrical support equipment, the test verified the performance of panels, consoles, cables, and the digital data acquisition system - all the electrical equipment that would be used to test the upper stages of the Saturn.15
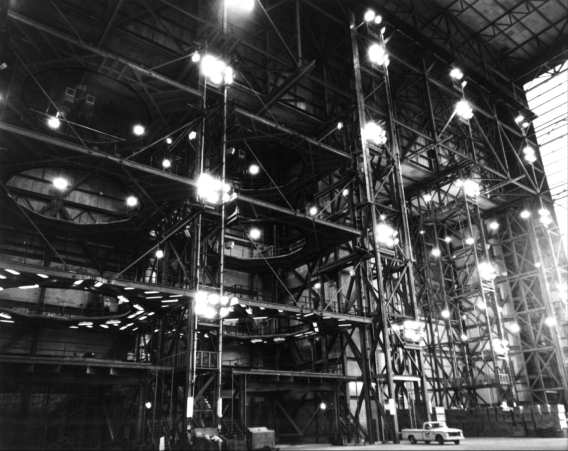
After checkout of all the support equipment, the launch vehicle teams began testing components and subsystems within the separate stages. The checkout of the first stage was performed on the mobile launcher in a high bay, while the upper stages were tested in the low bay cells. Technicians tested valves, electrical networks, radio frequencies, measuring instruments - all the items that made up the various systems within the stages. For example, North American conducted a “pressure transducer, potentiometer type systems test” that verified the performance of the S-II’s pressure transducers. (The Saturn’s transducers converted such things as temperature and pressure to electrical signals.) Before conducting the test, North American checked out the second stage’s digital data acquisition system and the connections to the assembly building’s measurement calibration station. Then, with stage instrumentation power on, readings were taken on each pressure transducer.16
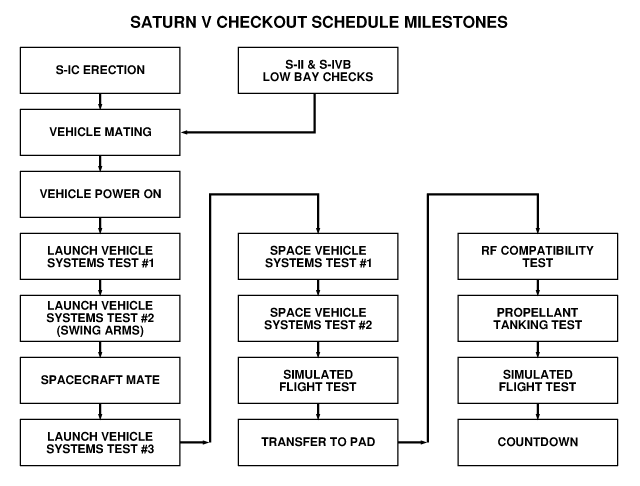
The erection of the launch vehicle in the high bay marked the first major milestone in KSC’s operations and prompted a series of tests such as the “S-IC - S-II electrical mate.” Three men, working eight hours, checked out the electrical interface between the two stages. Another stage test in the high bay was the “umbilical interconnect verification test, S-IVB flight stage.” Through a series of measurements, a Douglas crew verified the proper plug fit and electrical continuity between power sources on the swing arm and the S-IVB networks.17
The weeks after erection were spent in system and subsystem testing and in modifying the Saturn rocket. One day of Saturn activities illustrates the extent of the launch vehicle operation:
- Leak and functional test of the first stage nitrogen control pressure and purge system
- Checkout of the engine-bearing coolant valve
- Retest of the earlier engine-cutoff modification
- Engine leak checks
- Instrumentation system checkout
- Range safety receiver and decoder checks
- Guidance and control test
- S-IVB auxiliary propulsion system relay functional tests.18
When the various subsystems and systems procedures were completed satisfactorily, the launch team moved on to the Saturn’s integrated system tests.
The combined or integrated systems procedures tested vehicle functions involving several systems in one or more stages. These included the operation of the range safety command receivers and the Saturn’s destruct systems, the electrical interfaces of the combined vehicle, and the transfer from external to internal power. The flight sequence test took the launch vehicle past liftoff to exercise the switch selectors that keyed the flight systems. The emergency detection system test checked out the launch vehicle’s response to an abort situation. Since this system was one of the most intricate in the space vehicle, its test was one of the few automated for the Apollo 4 operation. The test employed an Apollo simulator and consisted of five parts: engine out, excessive rate (attitude), rate gyro, verification of the command module indicator, and a test of the vehicle’s abort logic plan.
The integrated tests on the launch vehicle culminated with the sequence malfunction procedures and the swing-arm tests. The former was actually a series of ten tests that ran a day or more. They verified the compatibility and operation of the launch vehicle and electrical support equipment in case of a malfunction and cutoff in the last seconds of the terminal count. For example, in test 5 the launch team would simulate a malfunction in the service arms just prior to their swinging clear of the vehicles. The test would determine whether the vehicle could shut down properly. The swing arm overall test verified the operation of all Saturn and ground support equipment systems during a normal firing sequence and on into flight. The test included the actual release of the hold-down arms, umbilical ejection, and the withdrawal of the swing arms and the tail service masts. Following the simulated liftoff, the flight computer directed the various switch selectors in the Saturn stages through the operation. The exercise terminated with the engine cutoff of the S-IVB stage and the issuance of propellant dispersion system commands.19
After the spacecraft joined the stack, integrated testing continued. Several tests, such as the emergency detection system procedure, covered familiar ground but now involved a complete space vehicle. The space vehicle overall tests 1 and 2 climaxed the test operations in the assembly building. Overall test 1, popularly known as “plugs in,” tested the electrical systems and some of the mechanical systems of the Apollo-Saturn, along with pertinent ground support equipment and range facilities, during a simulated normal liftoff and flight. The Saturn went through an internal power check while the spacecraft’s environmental control and navigation systems were checked out. After liftoff, the test simulated stage cutoffs as they would occur in normal flight. Overall test 2, the plugs-out test, came several days later. By actually releasing the hold-down arms and the umbilical plugs, this test verified that there was no electrical interference during the umbilical disconnect. In both tests the Saturn telemetering channels operated “closed loop” over lines back to the central instrumentation facility. The spacecraft operated its radio equipment “open-loop” to the Eastern Test Range and operation and checkout building. At the close of the plugs-out test, KSC and Marshall compared data on the Saturn’s operation with similar data collected during the swing arm and plugs-in tests.20
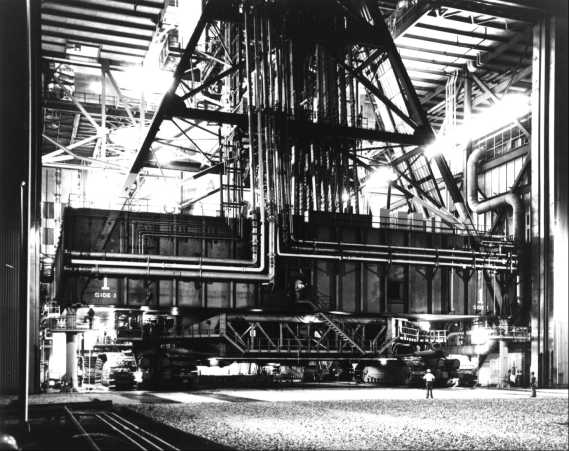
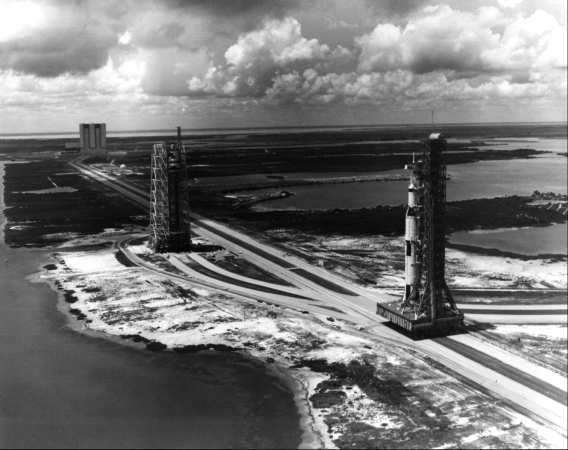
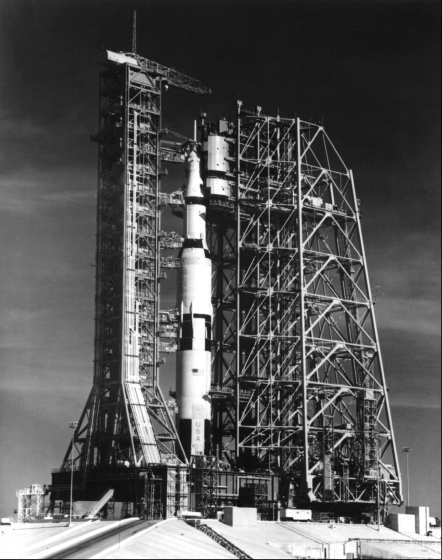
After the rollout to the pad, integrated tests, such as the “space vehicle power-on check,” verified the interface between the space vehicle and the pad facilities. The power-on test involved the ACE and RCA 110A automated checkout systems and the mobile launcher. [see chapter 16] A radio frequency compatibility test ensured that the pyrotechnic circuitry on the spacecraft would not be triggered by radio signals. This test was conducted in two stages, first with the mobile service structure around the Apollo, and then back at its parking site. The launch team ran another malfunction test at the pad and yet another check of the emergency detection system.21
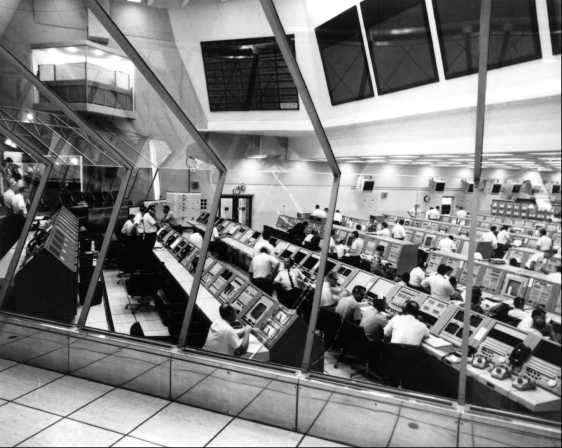
The flight readiness test represented one of the last major milestones. The test verified the proper operation of the space vehicle and associated ground support equipment before and after liftoff in a normal countdown, following terminal procedures as closely as possible. For this test the launch team brought the Apollo-Saturn as near as possible to its flight configuration. A minimum amount of test equipment was employed. Electrical circuits that could inadvertently damage the space vehicle were by-passed. The test conductor first ran the space vehicle through a simulated terminal count ending in a pad abort. A second run put it through tower clearance and ended with a service propulsion system abort and an earth landing for the spacecraft. After a second recycling of the count, the space vehicle flew a successful mission.22
Propellant loading tests came next, followed by the countdown demonstration test. While the flight readiness test focused on the space vehicle and its systems, countdown demonstration was intended to test the performance of the launch team and the ground support equipment. The objectives were to:
- Demonstrate the time phasing of the normal sequences necessary to prepare the space vehicle for launch;
- Verify that the space vehicle and support equipment were in a satisfactory status for launch as if launch were imminent, thus demonstrating the countdown procedure adequacy; and
- Verify propellant system integrity by loading the cryogenics.23
Like an actual 6-day countdown, the test was divided into a precount and a countdown. Spacecraft operations during the precount included powering up and testing the Apollo systems; servicing the liquid (water), gas (helium and nitrogen), and cryogenic (LOX and LH2) tanks; and installing pyrotechnic simulators. Two of the last actions were to stow spacecraft provisions and equipment and activate the service module’s fuel cells. At the same time the launch vehicle team turned on the Saturn’s power, tested electrical circuits, and installed batteries and ordnance items. Usually a hold would come at the end of the precount. These open periods provided the launch team a needed break, as well as time to make unscheduled corrections on the space vehicle.
At the beginning of the simulated countdown, the spacecraft team completed all work requiring access from the mobile service structure and removed it. Then the team continued with radio checks, the closeout of the command module, a hatch leak check, and a power transfer check. The launch vehicle team performed power-on and guidance system checks, loaded cryogenics, and tested the range safety command and other radio frequencies. Finally, with the ignition systems blocked to prevent an accidental launch, the terminal sequencer took the count to T-8.9 seconds where the test ended.24
The time required to prepare for a launch varied considerably during the Apollo program. As the trial run of the Saturn V and LC-39, everyone expected troubles with AS-501. On subsequent missions, however, the checkout took longer than KSC officials expected. A major reason was the condition of the flight hardware. NASA started with the premise that stages would arrive at KSC in a nearly flight-ready condition. The prelaunch checkout would require no more than four to six weeks in the assembly building and one week on the pad. Events proved otherwise. The launch vehicle and spacecraft contractors, beset by problems, delivered stages and modules that required extensive modifications. These changes contributed in large measure to the extended launch operations.25
KSC did not achieve a standard or routine for launch operations until the Apollo 9-11 missions, each of which required over five months. The receiving, inspection, and preliminary checkout ran four to six weeks for the S-II and S-IVB stages, one to two weeks for the S-IC and the instrument unit. After the launch vehicle was erected, subsystems tests took another month. Seven to ten days of integrated tests on the Saturn were followed by the erection of the spacecraft. A month more of tests in the assembly building culminated with the space vehicle overall test 1 (plugs in). Out on the pad, three weeks of tests preceded the flight readiness test. Propellant loading tests followed two weeks later. Several days thereafter KSC began the week-long countdown demonstration test that immediately preceded launch.26
More Delays for AS-501
Despite all the trials KSC had gone through with AS-501 by September, more were ahead. On 31 August the launch operations office issued a new schedule with the countdown demonstration test to begin 20 September. In less than a week the schedule was broken. When Boeing had to replace the hydraulic engine actuators on the first stage, Petrone’s office rescheduled the test for 25 September. A major milestone, the space vehicle malfunction overall test, was scrubbed on the 12th because of rain and high winds. The test team concluded the exercise the following day, but lightning slowed down operations on the 14th. For later flights the sequence would be flight readiness test, countdown demonstration test, countdown and launch. For the first flight of the Saturn V, however, the test directors wanted to have the flight readiness test as close to the launch date as possible and scheduled it after the demonstration test. KSC officials were not at all sure how well the new launch complex would perform. Events would justify their concern.27
The six-day countdown test started on the evening of 27 September. By 2 October the launch team was two days behind schedule. Following a hold, the test went smoothly from T-18 to T-13 hours, when computer problems forced another delay. The count reached T-45 minutes on 4 October when a computer, monitoring the propellant loading operation, failed. As a result 1,900,000 liters of kerosene and liquid oxygen had to be removed from the S-IC stage. The count, set back to T-13 hours, was resumed on 9 October. More computer problems and a faulty regulator on the helium gas system marred operations that day. By the time the count reached T-5 hours, the launch team was exhausted. Petrone called a two-day recess. Shortly after the test resumed on 11 October, a problem appeared with a battery heater on the S-II stage. As the battery could not be repaired or replaced quickly, another day’s work was cancelled. KSC finally completed the test on 13 October, after 17 frustrating days.28
As Paul Donnelly later noted: “In spite of the many problems encountered in the test, the crew had received an education that money couldn’t buy.”29 The launch date for Apollo 4 was postponed, pending the outcome of the test. After it was completed, few at KSC seriously believed that 501 could be launched on the new date of 7 November. Phillips acknowledged that “this is a target date. We are in a very complex learning process and we are going to take all the time we need on this first launch.”30 The growing concern of higher NASA management expressed itself at the flight readiness review on 19 October. The purpose of this meeting was to assess the readiness of the overall mission in general and the S-II in particular. Because it was unmanned, Apollo 4 was cleared for launch assuming the satisfactory completion of the remaining tests and modifications.31
The Launch of Apollo 4
KSC began an abbreviated countdown (56 1/2 hours) on 6 November 1967 pointing toward a 9 November launch. The propellant loading was a feat in itself; the propellant systems pumped 89 trailer-truck loads of LOX, 28 trailer loads of liquid hydrogen, and 27 rail cars of kerosene aboard Apollo 4. The day before the launch, representatives from the groups supporting the mission met at KSC for an informal review. The meeting gave Apollo 4 a “go” for launch, contingent on the resolution of a few minor problems.32
To recognize individuals who had performed in an exemplary manner on the manned spaceflight program, KSC invited Apollo contractors to select employees to visit the launch center for the liftoff. On 8 November, 43 of these “Manned Flight Awareness” honorees were guests of the center for a tour of facilities, a social evening that included a visit with six astronauts, and a view of the launch the next morning.
On the morning of 9 November, cars clogged the access roads as visitors filled every available spot. The countdown continued to its climax, when the five engines ignited. The small but astonishingly strong hold-down arms held back the giant ship for a few seconds. Suddenly the 36-story vehicle seemed to stand for an instant above the launch umbilical tower, and then it moved skyward with increasing speed. The bleachers at the press site shook, their light fixtures bounced, a flock of ducks changed course without breaking their V formation. Men shouted in triumph.
If distinguished guests in the stands to the northwest of the assembly building, the press corps, and the thousands of other visitors felt a sense of triumph, it paled before the feelings of the experts at their consoles in the launch control center. KSC’s last official act was Launch Operations Manager Paul Donnelly’s statement: “The vehicle has cleared the tower.” At that moment, responsibility left KSC’s hands. The Manned Space Flight team at Houston might refer back to Kennedy on specific problems for unmanned flights like Apollo 4, but in flights with men on board, corrections would come from the astronauts.
Wernher von Braun spoke of the mission as “an expert launching all the way through, from lift-off exactly on time to performance of every single stage.” General Phillips said:
I was tremendously impressed with the smooth teamwork that this combined government/multi-industry team put together. It was smooth, it was professional, it was confident. It was perfect in every respect. It was a powerful operation. You could almost feel the will with which it was being carried out. Apollo is on the way to the moon.33
During the course of the following week, George E. Mueller, NASA’s Associate Administrator for Manned Space Flight, put the success of Apollo 4 in focus. Noting the space age was ten years old, he said that the voyage of Apollo 4 dramatically increased the confidence of people across the nation and showed the maturing of a management structure that could administer the largest single research and development program ever undertaken in the Western world. He discussed the crucial flights of the lunar module coming in the near future and predicted that it would be possible for astronauts to land on the moon about the middle of 1969.34
Press, VIPs, Tourists, Dependents
Elaborate plans for the reception of guests paid off both at the launch of Apollo 4 and at the 13 subsequent Apollo launches. Five days before the launch, the Office of Public Affairs had opened a news center on the 10th floor of the Cape Royal Building in Cocoa Beach. The news center issued badges to representatives of industry and the news media, including TV technicians, for access to the space center. Bus tours of the entire center were conducted twice daily for reporters and photographers. Starting twelve hours before launch time, three NASA buses operated a shuttle service every half hour between the Cape Royal and the LC-39 press site. The last bus departed one hour before launch time, but by then most media personnel were in their seats on a “first-come, first-served” basis. Southern Bell installed 360 telephones at the press site, with the news organizations paying individually for service. A mobile food service unit supplied hot snacks.35
The news center held status briefings on the mission twice daily preceding the launch. The day before the launch, there were two press briefings at launch complex 39, followed by a tour of pad A. The afternoon mission briefing took place at the news center itself. John W. King, chief of the Public Information Branch, provided countdown commentary, starting five hours before liftoff. Loudspeakers carried this commentary to the press site at LC-39, the VIP site on the opposite side of the vehicle assembly building, the visitors information center, the KSC news center, all cafeterias throughout KSC, and the main buildings in the industrial area. The Manned Space Center in Houston took over the commentary after liftoff.
The Cape Royal auditorium was available to contractors for presentations at times not in conflict with NASA requirements. Contractors’ representatives could schedule such events in advance with the approval of the KSC news center manager. The contractors also had space for displays and a liaison desk for their public relations representatives.
At least equally important, but more complicated than preparations for representatives of the media and the contractors, was the task of caring for the dignitaries who would descend on the area as long as viewing an Apollo launch would be a socially and politically prestigious event. NASA Headquarters had its own list of invitees, as did the three centers (Kennedy, Marshall, and Houston). Naturally many names were duplicated on the lists. The centers settled the overlapping among themselves, and each center director invited his guests personally. The distinguished visitors viewed the launch from uncovered bleachers northwest of the assembly building, which could accommodate 1,000 guests.
Protocol representatives from NASA Headquarters, KSC, Marshall, and the Air Force Eastern Test Range set up a joint protocol center at the Sheraton Cape Colony Inn in Cocoa Beach, five days before liftoff. With the usual foresight, KSC had a contingency plan that did not have to be used on Apollo 4. In case of postponement or delay of a launch, the guests automatically had a valid invitation for the rescheduled time. In the meantime, the Protocol Office would provide further tours of the Kennedy Space Center until launch. NASA and contractor employees at KSC could view the Apollo 4 mission from a convenient area near their place of duty. Their dependents watched from Avenue E in the industrial area, south of the Apollo training facility. The Security Office provided badges, car passes, and instructions five days before the launch. Some contractors and range organizations chartered buses to bring dependents to the viewing site. Throughout all viewing areas, KSC provided emergency first aid and ambulance service. Security handled parking of vehicles and controlled traffic with an ease that was to grow with each launch.36
KSC Learns about Government Accounting
While KSC was wrestling with the protracted checkout of Apollo 4, its top management had to divert considerable attention to a U.S. General Accounting Office (GAO) audit that had started two years before and now reached a climax. Back in the spring of 1965, while KSC was still in the process of readying launch complex 39, the GAO began an audit of the contract for a second crawler-transporter. It wanted written studies substantiating the need for two vehicles. Close to five months after beginning its audit, the GAO informed KSC Director Debus that the evidence had “thus far eluded” it.37 Debus replied on 15 October 1965 that such documentation did not exist - a surprising fact in view of the detailed documentation of almost every activity at the Cape. Debus pointed out that a second crawler was critical to the unit’s performance because of the possibility of a breakdown, and that NASA had informed Congress and the Bureau of the Budget of its plans to purchase two transporters.38
Six months later, on 14 April 1966, the GAO notified Debus of its plans to examine other duplicate facilities on LC-39. Stanley Dyal, the auditor-in-charge, met with KSC officials and toured LC-39. On 6 July the GAO asked Debus about the decision to construct mobile facilities for six launches a year, in view of NASA and contractor studies that showed the mobile concept to be more economical only above a rate of 12-18 launches a year. Since NASA Headquarters had made the decisions the GAO questioned, Debus referred the letter to Washington. On 16 August 1966, Associate Administrator Mueller replied to the GAO, pointing to the presidential declaration on space of 1961 and the desire for sufficient flexibility to meet future needs, and adding that complete documentation of all studies, analyses, and conferences was not available.39
After a visit to KSC in late August 1966, the Associate Director of the GAO, Clerio P. Pin, decided to send Dyal from the Atlanta office to review what studies were available. For two months, Dyal read the extensive documentation pertaining to alternate methods of developing launch complex 39. When he departed on 28 October, Dyal stated that the GAO office in Washington would handle further inquiries at NASA Headquarters.40
Upon completion of the audit in June 1967, the GAO sent a 39-page draft report of its findings to NASA Administrator Webb, requesting comments and inviting discussion. A week later, NASA Headquarters transmitted the report to KSC for comments. Even though preparations were under way for the first flight of the Saturn V and the first operational use of LC-39’s mobile facilities, KSC undertook an intensive month-long analysis of the validity of the GAO statements. Background documents relating to early decisions were researched and cost figures were reviewed. Almost every office involved in any way with launch complex 39 participated in the analysis. The GAO report was based on records at NASA Headquarters and KSC, as well as numerous industry and in-house studies made between 1961 and 1967. The report also indicated a shift from the initially announced purview of the audit - the concern about duplicate facilities - to focus on launch complex 39 and an analysis of whether or not NASA had “adequately considered the relative operational and cost merits of both mobile and conventional launch facilities.” It accused NASA of failing to keep Congress informed on important matters and of using obsolete data in supporting its budget proposals.41
In preparing a response to the GAO report, Debus wrote NASA Headquarters on 19 July 1967 that the GAO had worked from inaccurate assumptions and arrived at erroneous conclusions. In the report, computed savings were based on outdated analyses. Debus asserted that KSC had kept Congress informed on all major issues, and that members of Congress had concurred with KSC’s rejection of conventional launch facilities in favor of the mobile concept. At a meeting between representatives of NASA and GAO on 8 September 1967, NASA agreed to hold its response in abeyance until the GAO was able to review new documents.42
Queries continued to come in, and during October threatened to disrupt some KSC operations. NASA Headquarters asked KSC to comment on a statement that would be submitted to GAO the following month. Admiral R. O. Middleton, KSC’s Apollo Program Manager, said that some of the key personnel who were being called on to answer the GAO queries were working overtime in preparation for the Apollo 4 mission. He recommended that KSC make no response until two or three weeks after the launch. KSC acceded to the request, however, completing a reply one week before the Apollo 4 launch. Headquarters used some of the comments and added many of its own in a communication to GAO two months later. In a letter of 24 January 1968 accompanying NASA’s response, Harold B. Finger, Associate Administrator for Organization and Management, pointed out that the Apollo 4 flight had tested Saturn V-Apollo launch complex 39 and demonstrated that the United States now had a capability to launch large rockets. The choice of the lunar orbital rendezvous, the stress on ground tests in lieu of flight tests, and the successful flights of the Saturns had greatly reduced the number of launches anticipated at the time launch complex 39 had been planned.43
On 27 March 1968, after almost three years of reviewing the mobile concept facilities at LC-39, the GAO informed NASA that it planned no further investigations. Although this meant that it would not submit the report to Congress, the GAO offered NASA some precautionary advice. The review of some of KSC’s planning studies convinced the auditors that fixed facilities could have been constructed at a saving of $55 million for a launch rate of 12 or less per year. The GAO would continue to make “reviews of this nature” in view of NASA’s large expenditures. It suggested that NASA document all major decisions in a manner that would show clearly the basis for the actions at the time of the decision, and that NASA make all related files available at the start of future reviews. Finally, the GAO expressed hope for better communications with NASA.44
Although the audit diverted much effort to actions that contributed little if anything to the accomplishment of the manned lunar landing, it was not unproductive. By re-emphasizing the need for thorough documentation to support management decisions, the audit increased awareness that, in spite of the pressure of KSC’s mission, the center had to remain responsive to periodic audit by the “government’s financial watchdog” and had to manage its records toward this end. NASA Headquarters, on its part, hoped that the GAO had become more aware that NASA based its decisions on significant technical factors, in addition to management and cost aspects. NASA also hoped that GAO’s constructive suggestions might help prevent such time-consuming, expensive reviews in the future.45
The GAO had questioned NASA’s judgment on administrative decisions such as the evaluation of costs, technical decisions dealing with operational effectiveness, and communications between NASA and Congress. The complaints arose chiefly from the GAO’s reliance on early planning documents, while NASA had used an evolving series of planning studies that kept pace with new developments. In other words, the GAO saw the early planning studies as an end product, whereas NASA saw them as the first step in a process. Also GAO had the advantage of hindsight. The decisions concerning the mobile concept had been made in the light of contemporary knowledge, at a time when experts were calling for upwards of 50 launches a year.
NASA’s reply clearly indicated that it viewed the manned lunar landing program as an embarkation point, not a terminus. It cited 1963 statements to Congress by James E. Webb wherein the Administrator asked for a position of preeminence in space, and the more explicit one by D. Brainerd Holmes that called for “landing on other astronomical bodies.”46 The National Aeronautics and Space Act of 1958 lent support to this interpretation. The GAO, on its part, drew a distinction between what the government had authorized and what NASA planned or anticipated. In the broad sense, the GAO had zeroed in on the time-honored practice of government organizations trying to expand beyond immediate authorizations. A rigid adherence to authorized programs without thinking of the future might well have placed NASA in a strait jacket. It would have forced NASA to revert to the abandoned practice of constructing a special facility for each type of launch vehicle, something that members of Congress had hoped to prevent. It would also have restricted the speculation and experimentation necessary for progress.
KSC came out unscathed, except as regards its documentation of management decisions. This was paradoxical in view of KSC’s extraordinary devotion to technical documentation. One could argue, as Harold Finger did, that a new organization must give priority to accomplishing its mission and defer paper work to a later date. But this could hardly satisfy the GAO, which by one means or another habitually reminded government organizations that the appropriation of funds is a beginning and not an end, and that they must one day answer for the use of those funds.
ENDNOTES
- OMSF, Apollo Program Flight Summary Report, Apollo Missions AS-201 through Apollo 8, pp. 13-17; MSFC, Technical Information Summary, AS-501, Apollo Saturn V Flight Vehicle, R-ASTR-S-67-65, 15 Sept. 1967.X
- "NASA Announces Changes in Saturn Missions,” NASA release 63-246, 30 Oct. 1963.X
- Dir., Apollo Program, “Clarification of Apollo Saturn IB and V Flight Mission Designations,” 12 Apr. 1965.X
- MSFC, Technical Information Summary, AS-501, pp. 24-75.X
- OMSF, Apollo Program Directive No. 4D, 1 July 1966; No. 4E, 22 Sept. 1966; No. 4F, 30 Nov. 1966; Proffitt interview; NASA, Sixteenth Semiannual Report to Congress, 1 July-31 Dec. 1966, pp. 49, 51-52. See also NASA, Seventeenth Semiannual Report to Congress, 1 Jan.-30 June 1967, p. 11, for information on the spacer.X
- KSC,"LC-39 Site Activation Status Report,” 14 Sept. 1966; Spaceport News, 15 Sept. 1966; KSC, “Apollo 4 (AS-501) Daily Status Reports,” Sept.-6 Oct. 1966.X
- KSC, “Apollo 4 Daily Status Reports,” 29 Nov., 1, 2, 6, 7, 13 Dec. 1966.X
- Ibid., Dec. 1966 and Jan. 1967; KSC, “Program Milestone Data - Apollo,” 15 July 1971.X
- KSC, “Apollo 4 Daily Status Reports,” Feb.-Mar. 1967 (see 16 Mar. for number of wiring discrepancies in spacecraft); NASA, Seventeenth Semiannual Report to Congress, 1 Jan.-30 June 1967, pp. 11-12.X
- 10. Spaceport News, 3 Mar. 1966; Fowler interview.X
- KSC, “Apollo 4 Daily Status Reports,” Feb. 1967; Spaceport News, 15 Feb. 1968.X
- KSC, “LC-39 Site Activation Status Report,” 19, 26 Apr. 1967.X
- NASA release 67-132, summarized in Astronautics and Aeronautics, 1967, p. 164; KSC, “Apollo 4 Daily Status Reports,” May-Aug. 1967; Spaceport News, 31 Aug. 1967.X
- KSC, Catalog of Launch Vehicle Tests, Saturn V, Apollo/Saturn V, Revision 1, 15 June 1966, GP-244.X
- Ibid., p. 1-27; Carlson interview, 5 Sept. 1974.X
- KSC, Catalog of Launch Vehicle Tests, Saturn V. p. 2-18.X
- Ibid., pp. 1-18, 1-28.X
- KSC, “Apollo 11 (AS-506) Daily Status Report,” 25 Mar. 1969.X
- Catalog of Launch Vehicle Tests, Saturn V, pp. 7-1 through 7-13.X
- Ibid., pp. 9-1 through 9-43; KSC, Apollo/Saturn Program Development/Operations Plan, 2: 3-90 and 3-93 provide a comparison of the two tests and their objectives.X
- KSC, Catalog of Launch Vehicle Tests, Saturn V, pp. 9-1 through 9-43.X
- Ibid., pp. 9-21 and 9-25.X
- Ibid., p. 9-3.X
- Ibid.; Donnelly interview, 19 June 1974.X
- Harris interview; Carlson interview, 5 Sept. 1974.X
- KSC, “Program Milestone Data, Apollo,” 6 June 1973.X
- KSC, “Apollo 4 Daily Status Reports,” Sept. 1967; Donnelly interview, 19 June 1974.X
- KSC, “Apollo 4 Daily Status Reports,” 27 Sept.-13 Oct. 1967; Richard S. Lewis, Appointment on the Moon: The Inside Story of America’s Space Venture (New York: Viking Press, 1968), p. 406.X
- Donnelly interview, 19 Nov. 1970.X
- NASA release 67-274 and Baltimore Sun, 26 Oct. 1967, p. A6, summarized in Astronautics and Aeronautics, 1967, p. 319.X
- Phillips to Mueller, memo for record, 5 Sept. 1968; KSC, “Apollo 4 Daily Status Reports,” 19-20 Oct. 1967.X
- Spaceport News, 23 Nov. 1967.X
- Ibid.X
- Ibid.X
- KSC Information and Protocol Operations Plan - Apollo 4 Mission, pp. 1-4.X
- Ibid.X
- J. E. Ballou, GAO Area Audit Mgr., Atlanta, to L. Melton, KSC, 30 Mar. 1965; Aviation Week 89 (23 Sept. 1968): 74; H. L. DeLung, Acting Regional Mgr., GAO, Atlanta, to Debus, 20 Aug. 1965. The authors recognize their reliance on thorough researches of Maj. James J. Frangie in this section.X
- Debus to DeLung, 15 Oct. 1965.X
- R. J. Madison, Mgr., GAO Regional Off., Atlanta, to Debus, 6 July 1966. See also p. 16 of draft report, Comptroller General of the U.S., “Review of Launch Complex 39 Facilities for the Saturn V Vehicle, John F. Kennedy Space Center, Florida, NASA,” undated, accompanying letter of Clerio P. Pin, Assoc. Dir., GAO, to Webb, 8 June 1967 (hereafter cited as “GAO Draft Report, KSC, 1967"); Mueller to William Parker, Asst. Dir., Civil Accounting and Auditing Div., GAO, Washington, 16 Aug. 1966.X
- Melton, memo for record, 29 Aug. 1966; Malcolm S. Stringer, memo for record, “GAO Review of Justification for Redundant and Duplicate Launch Complex 39 Facilities, 31 Oct. 1967,"X
- Raymond Einhorn, Dir. of Audits, to Debus, “GAO Draft Report on Review of Launch Complex 39 Facilities for the Saturn V Vehicle, KSC, NASA,” 13 June 1967; “GAO Draft Report, KSC, 1967,” p. 24.X
- Debus to Mueller, 19 July 1967, in NASA Hq. History Office; Einhorn to Debus, 15 Sept. 1967.X
- Raymond Middleton to KSC Liaison Representative with GAO, 30 Oct. 1967; Melton, memo for record, 19 Oct. 1967; Debus to Mueller, 2 Nov. 1967, in NASA Hq. History Office; Harold B. Finger, Assoc. Admin. for Organization and Management, to Clerio P.. Pin, Assoc. Dir., GAO, Washington, 24 Jan. 1968, with enclosures, pp. 10-12, NASA Hq. History Office.X
- Pin to Finger, 27 Mar. 1968, in NASA Hq. History Office.X
- Stringer interview; Finger to Pin, 24 Jan. 1968, NASA Hq. History Office.X
- House Committee on Science and Astronautics, 1964 NASA Authorization, 88th Cong., 1st sess., 1963, pt. 1, p. 5; pt. 2, pp. 126-27.X